Materials:
The following materials can be epilamized: metals, plastics, ceramics, jewels, elastomers, duroplasts, glass. Fluorized materials like PTFE cannot be epilamized.
Fields:
Precision mechanics, micromechanics, nanotechnology
Technological fields:
Automotive, watches and clocks, instruments, space, aero-engineering, medical technology, optics
Components:
Sliding bearings, axles, gear wheels, guides, roller bearings, plain bearings, seals, contact washers, housings, shafts, porous sinterbearings, collectors, switches, plugs, plug connectors, relays, contacts, lenses, mirrors, sensors
Targets for improvement:
For-life lubrication, noise damping, guaranteed functionality, avoidance of long-term damage, optimisation
People with responsibility for electromechanical and electronic components have already started considering epilamizing all the safety-related components in the machining process in order to avoid the likelihood of S.I.F. (surface infecting fluids) problems occurring later. This would enable the reliability of motor vehicles, for instance, to be improved further.
Lubricants used in the industrial sector today have to deliver an extremely broad performance spectrum. In addition to the actual tribological criteria such as the reduction of friction and wear, there is also a growing requirement to satisfy environmental conditions which just 10 years ago could not be satisfied. For instance, one such condition is temperature range. In the motor vehicles industry nowadays lubricants (these may be oils or greases) are used for lubricating the widest possible range of different bearing material which must be able to ensure safe functioning right through from -40 to +160°C with the additional requirement that they must generate the smallest possible amount of internal friction. Most importantly, at high temperatures problems occur with lubricants creeping. In this case epilamization is essential.
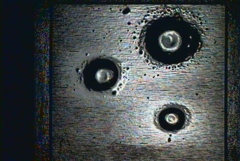
The wetting rate depends on viscosity and time.
Highly viscous fluids creep just as far, but more slowly.
Greases are depleted of oil.
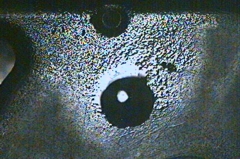
Impregnating fluid for porous sinterbearings. The oil component wets.
The thickener remains.
Strength of the epilame layer
The resulting layer is extremely thin, approx. 0.00001 mm. It is invisible to the naked eye and cannot be proved to exist without test fluid.
Angle decoding gear. Optical sensors can also be epilamized. This will prevent contamination by agglomerating particles.
Safety measures (coating components)
Epilamizing the surface of a solid body.
Epilamization is an effective method for solving the technical problem of creeping; epilamization involves reducing the apparent surface tension of components by applying a film which reduces the surface tension. This method has been known for around 100 years in the field of precision mechanics, and over the last decade has also been brought in with "normal" mechanical engineering. Epilamization is a chemical process that prevents or restricts the spreading out and creeping of oils on metal and plastic surfaces. By using fluoractive polymers which form a barrier layer, an oil-repellent effect is achieved which is effective for virtually all the different lubricants used in technical applications.
This effect results from reducing the apparent surface tension of the solid body by polymerizing a fluoractive layer of plastic with a low surface tension. The effect on surface tension can be detected even in extremely thin layers. In laboratory tests, epilam coatings of a few hundred molecules in thickness demonstrate a considerable reduction in apparent surface tension.
Effect of viscosity:
As the temperature increases, so the viscosity (viscidity) of a lubricant is reduced. The surface tension is also reduced at the same time. Both of these effects speed up the wetting.
What the coating can withstand
The thermal resistance of epilam coatings is from -70 to +200°C. The coating's resistance to mechanical abrasion is comparable to that of a very thin coating of resin paint. Epilamized surfaces are dry and can withstand normal handling in a production process with no ill effects. The coating can only be removed mechanically, i.e. by machining the surface, or by very lengthy ultrasound treatment in a suitable solvent.
Service life of the coating
In principle there is no limit to the service life of an epilam coating. It behaves in a similar way to PTFE. Its effectiveness can be reduced if liquids condense on it or if dust is allowed to build up. Epilam coatings have long been used for instruments in motor vehicles where they have performed well for more than 20 years.
Effectiveness with different lubricants
The epilamization agents we have developed are effective against almost all lubricants. The only exceptions are fluorized lubricants and lubricants with a large wetting agent content. Fluorized materials (elastomers and PTFE) cannot be epilamized.